Factory Layout Optimization: 5 Powerful Tips for Maximum Productivity
Optimize your factory layout with tips to boost efficiency, reduce waste, and streamline workflow. Discover lean principles, tech tools, and production planning strategies.
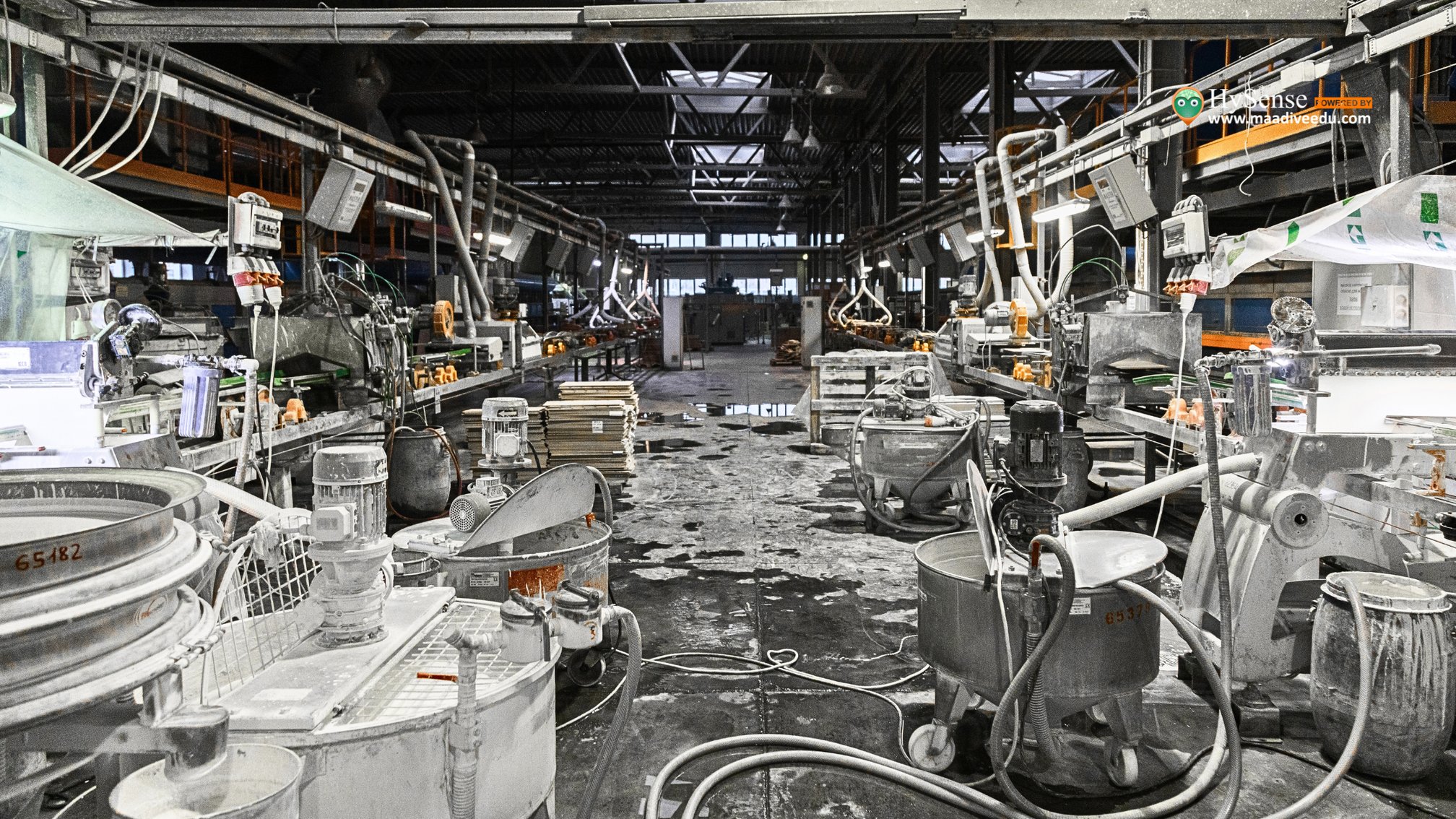
Table of Contents
Introduction to Factory Layout Optimization
Optimizing your factory layout is all about making your manufacturing space work smarter, not harder. A well-planned layout allows workers, materials, and equipment to flow efficiently, cutting down on wasted time and effort. This helps increase productivity, reduce costs, and improve the overall output of your operations.
In today’s fast-changing manufacturing world, getting your factory layout right is more important than ever. With effective planning and small, meaningful changes, you can turn your workspace into a powerhouse of efficiency. Let’s dive into five simple yet impactful tips to help you optimize your factory layout. know more
1. Assess Your Current Manufacturing Layout
Evaluate Space Utilization
The first step in improving your factory layout is taking a good, hard look at how you're using your space. Are there areas that are crammed with equipment and difficult to navigate? Or spaces that seem empty and underused? Every square foot of your factory should be contributing to production. For instance, if you find a storage area that's too large, you could reallocate part of it for additional workstations.
Identify Workflow Inefficiencies
Once you’ve examined your space, the next thing to tackle is your workflow. Think about how materials move through your factory and how workers interact with the equipment. Are there areas where things slow down because employees are waiting for supplies or equipment to become available? Or are workers walking long distances to fetch tools?
For example, imagine a workstation where a worker has to walk across the room several times a day to retrieve parts. By moving the parts closer, you can save time and energy, making your factory more productive. Fixing such inefficiencies is like smoothing out wrinkles in your processes.
2. Implement Lean Layout Principles
Understand Lean Layout Concepts
Lean layout principles are all about cutting out waste and focusing on what truly adds value to your operations. Waste doesn’t just mean leftover materials—it can also mean wasted time, unnecessary movements, or over-complicated processes. Lean practices simplify everything, making work easier and faster for everyone.
Apply Lean Principles in Your Factory
Start with the 5S system:
- Sort: Get rid of items you don’t need.
- Set in Order: Arrange everything neatly so it's easy to find and use.
- Shine: Keep your workspace clean and clutter-free.
- Standardize: Make these practices part of your daily routine.
- Sustain: Stick to these habits over the long term.
Reorganize your factory to ensure each step in the process flows smoothly into the next. For example, set up assembly lines so workers can hand off parts quickly without extra trips. Tools and equipment should be placed within arm’s reach to minimize movement.
These small changes, when added up, can have a big impact on your productivity.
3. Incorporate Advanced Technology
Leverage Technology for Layout Optimization
Modern technology can make your factory layout smarter and more efficient. Imagine robots handling repetitive tasks or sensors that warn you before a machine breaks down. These innovations help save time, reduce errors, and keep your factory running smoothly. know more
Examples of Technological Integration
One popular technology is Automated Guided Vehicles (AGVs)—these are like little robot carts that transport materials across the factory. They save workers from having to carry heavy loads and ensure materials are always where they need to be.
Another game-changer is digital twin technology, which lets you create a virtual model of your factory. With it, you can test changes to your layout without disrupting operations in real life. Want to see how adding a new machine might affect your workflow? Test it digitally first!
By embracing technology, you not only modernize your factory but also ensure it operates at its full potential.
4. Optimize Production Floor Planning
Strategies for Effective Production Floor Planning
A factory floor that’s well-organized leads to fewer delays and smoother operations. This means planning your layout so materials, workers, and equipment can all move effortlessly. For instance, think about the path materials take from delivery to storage, and then to the workstations. If this path isn’t direct, it could be slowing you down.
Create a Balanced Layout
A good layout balances productivity with comfort and safety. For example:
- Ergonomic Workstations: Design spaces that reduce strain on workers. Adjustable tables and chairs, for instance, can prevent fatigue.
- Efficient Material Handling: Use conveyors, trolleys, or even simple carts to make moving materials easier and quicker.
- Buffer Zones: These are small storage areas between processes that help absorb unexpected delays or variations in production speed.
By carefully planning your production floor, you ensure everything runs like a well-oiled machine.
5. Regularly Review and Adjust Your Layout
The Role of Continuous Improvement
Just because your layout works well now doesn’t mean it will be perfect forever. As your production grows or new technologies become available, you’ll need to adjust. Regularly reviewing your layout helps you keep up with changes and stay efficient.
Conduct Layout Audits
Make it a habit to assess your factory at least once or twice a year. Look at metrics like how much downtime you’re experiencing or how quickly products move through each stage. Don’t forget to ask employees for feedback—they often have great ideas about what could be improved since they’re working in the space every day.
For example, a worker might suggest moving a frequently used tool closer to their workstation. Small changes like this add up over time and lead to big gains in efficiency.
Conclusion
Optimizing your factory layout doesn’t have to be overwhelming. By following these five tips—assessing your current setup, applying lean principles, leveraging technology, planning your production floor wisely, and regularly reviewing your layout—you can create a space that’s efficient, productive, and adaptable to future needs.
Every improvement, no matter how small, contributes to a smoother workflow, better space usage, and happier employees. Over time, these changes will help your business grow and remain competitive in the fast-paced manufacturing world. So start today—step by step, transform your factory into a productivity powerhouse!
Follow us for more insights and updates on transforming your factory into a powerhouse of efficiency and innovation.